The really odd thing is that casting is a very cheap hobby. I have less than $100 invested in my furnace, and about the same in the sand.
The furnace is an old barbecue grill I recycled. (the top was aluminum, and has been melted down already). The grills went on the bottom of the cart for the furnace to sit on. The furnace itself is a couple of $5 buckets from Home Depot, lined with homemade insulating refractory cement. Basically some fireplace cement from the local brick place, mixed with some play sand and perlite, both from Wal-Mart.
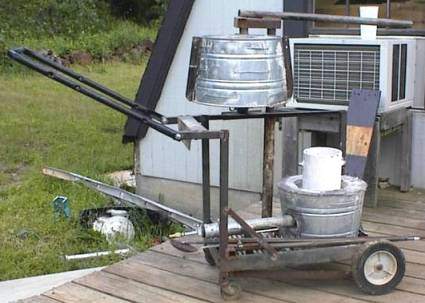
The burner is an assembly of pipes from the local hardware store. I used a cheap air hose from Harbor Freight, with an acetylene regulator from my cutting torch. The propane bottle I had.
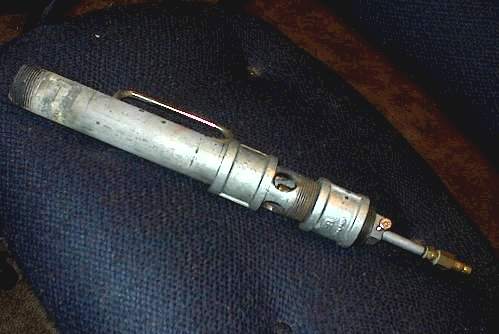
The crucible for melting the aluminum in is a piece of steel pipe cut from my scrap pile, with a plate welded to the bottom. As you can see from the picture, it is lined with what is called "kiln wash". This is some kind of clay solution, it helps keep the steel from oxidizing, and also keeps it from contaminating the aluminum.
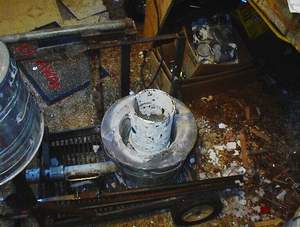
The tongs for picking up the crucible were also welded up from scrap.
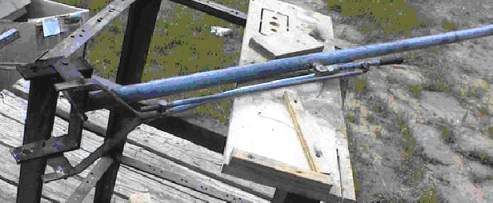
Built me a pyrometer for about $30, to take the temp of the liquid aluminum. Turns out aluminum is easy to melt, but not that easy to cast. If you pour too cold it doesn't flow right, and if you pour too hot, you get shrinkage, contamination, and gas problems. You can't tell the temp of liquid Al by looking at it like you can with most other metals, either. If you can see it glow, it's too hot to pour!
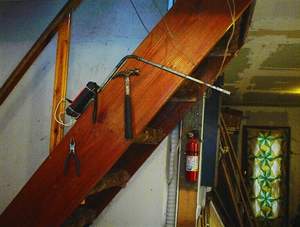
My biggest purchase was the special oil bonded sand. The sand wasn’t that expensive, but you try shipping a 100lb box of sand! Though I had passable results using playsand and cat litter for "green sand", the finish from the oil bonded sand is SO much nicer.
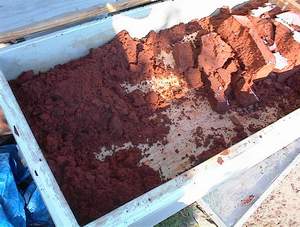
Now, I didn't come up with all this myself. As with boat building, there are a ton of sites on the 'Net, and several egroups, dealing with nothing but home hobby casting. Some links:
https://www.host33.com/casting/
https://groups.yahoo.com/group/hobbicast
https://www.rockisland.com/~marshall/foundry.html
https://www.webpak.net/~rreil/design.html
I'm slowly collecting parts for the next furnace. This one will be for casting bronze. Maybe even for casting IRON.
Hey, maybe someday I'll even fix the outboard! |