In July 2000 I received an order for a set of plans for a Shuttle
31 to be built in Western Red Cedar strip planking with Epoxy
and glass reinforcing. I had been in correspondence with the
teacher of a group of young people at a Waldorf (Steiner) school
in Switzerland.
This teacher, Thomas Wolf, intended to head up a team of 12
students with the aim of building two 31 ft cats in less than
two years.
At the start of the project the students wrote to me “We
are twelve students at the age of 16-17 years. We attend a Waldorf
school in Muttenz, Baselland. Two afternoons per week we work
at the boats. While our schoolmates attend special courses like
working on a farm, we will solely concentrate on building the
boats. Also during the holidays we will sacrifice some weeks
for the project.”
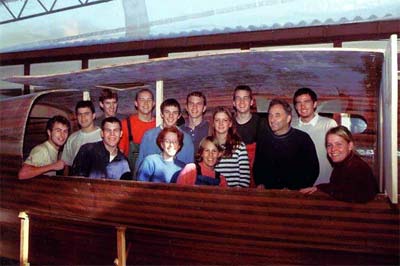
When they finished building they planned to sail the boats
down the Rhine into the North Sea, and on to the Mediterranean,
where the boats were to be based. They would also be involved
in raising sponsorship, and producing a web site, and would
all get their Swiss equivalent of the yacht masters certificate,
so that they could skipper the boats when taking out other students
on environmental educational cruises in Elba.
I thought it was an amazing project for a group of students,
and I knew that there was a lot to learn and do in less than
two years. I sent off the plans and the project began.
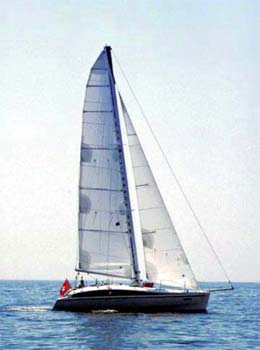
I was never in any doubt that the boats could be built. The
Shuttle 31 is ideally suited to strip planking in either Core-Cel
foam or Cedar, and the plans are very detailed. I provide backup
as part of the package, and my experience with homebuilders
indicated that my plans are so detailed that there are often
only a few points to clarify along the way.
The web site www.fossailing.com
duly appeared which meant that we could follow progress on the
site. As the months went by the boats took shape and looked
very good. Questions would arrive by Email, and the students
who spoke English best undertook the task to communicate with
me. Thomas Wolf’s son Florian, took a key role in the
project even though he had left the School to undertake further
qualifications elsewhere.
I am sure that the design would have provided considerable
interest to the students from a technical point of view.
Although it is relatively straightforward to build one of these
boats, there is a wealth of technical thinking and detail in
the drawings which would have provided a lot of additional learning
opportunities for the students in understanding the loads in
the boat and how the structure is made to take them. So they
would not only be learning craft skills, but they would also
be developing an understanding of how to think about structures.
Dale Schnieder told me that one of the highlights of building
my designs is that the technical aspect is so interesting, and
that his building team particularly enjoy this aspect of building
the boats. Once the ideas behind where I place the fibres, becomes
clear the whole design concept makes sense in quite a straightforward
way. This makes the boats very interesting to build.
The actual building process
The first task was to build the mould frames from the full
size computer lofted patterns I provide, and set them up on
a strongback at the correct station spacing. For the Cedar boat
I suggest building the hull on the outside of the hull lines.
This has the effect of adding 15 mm to the hull and increases
the buoyancy to account for the added weight of the wood.

The frames are made from 20 mm MDF or cheap plywood. Once
they are set up the hull planking begins. 50 mm wide strips
of Western Red Cedar were edged glued and screwed to the frames.
Eventually the screws are removed and the holes are filled with
epoxy during the glassing stage. Details of this method can
be found in “The
Gougeon Brothers on Boatbuilding” Pendell
Printing Inc. ISBN 0-87812-166-8.
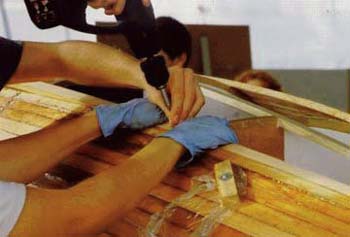
The planks are fitted
carefully before gluing, and the hull shape develops very quickly.
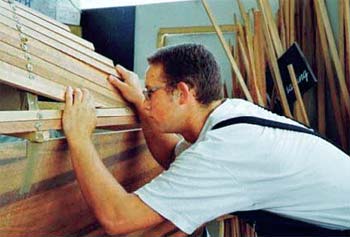
When the hull is fully planked the surface is sanded to a
smooth fair finish with a coarse sandpaper. One layer of biaxial
glass is applied all over the outside of the hull, and
extra reinforcing is added as shown on the plans.
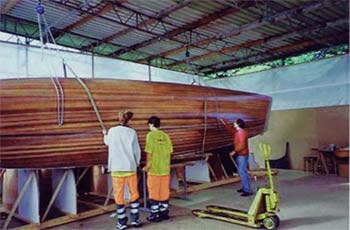
The fibre direction is important, for the ”integrated
structure” and arrows on the plan show how to lay up the
layers. Once the glassing is complete, the hull is sanded. Finally
the hull is lifted from the mould and set into a cradle. The
Fossailing team decided to split the hull and deck at the sheer
line, and so the decks ware built separately.
The photo below shows the students laminating the biaxial glass
into the inside of the deck. By taking care at this stage, the
team achieved a surface that was good enough to leave as the
final interior finish.
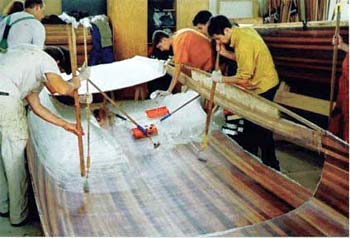
This has meant that the inside of the boat has a lovely wooden
feel.
The photo below shows the deck glassed on the inside and outside,
ready to fit to the hull. Figure 8 shows the inside as the deck
is fitted. The edges are glued together, and layers of biaxial
glass are laid along the join, inside and out.
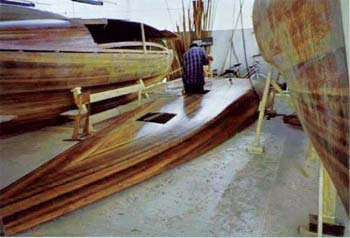
Bulkheads can be made ahead of time, In this design they can
be plywood or foam sandwich. The Fossailing team decided on
foam sandwich and the next photo shows the first bulkhead cut
out and ready to be glassed and then fitted in place.

Bulkheads are attached to the hull with an epoxy fillet, and
layers of 45 degree glass fibre.
The drawings show how each panel is connected into the hull,
with the exact width and weight of glass required. These connections
can be laminated on a plastic sheet outside the hull, and then
the whole connection is laid into the corner 2 ft lengths.
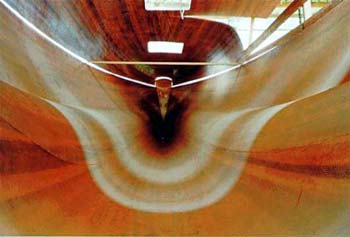
This method reduces the mess that can occur when glassing
in the interior components, and allows for better resin to glass
ratios. Keeping the hull clean inside means less time spent
at the final finishing stage.
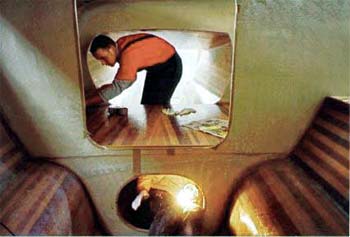
The finished hulls can be seen in the next photo. Note the
added foam bows for protection against collision. On impact
the foam bow is designed to collapse back to a strong wooden
bulkhead about 300 mm back. This absorbs the load and should
prevent flooding. If the wooden bulkhead is breached, there
is another watertight bulkhead 6 feet further back.
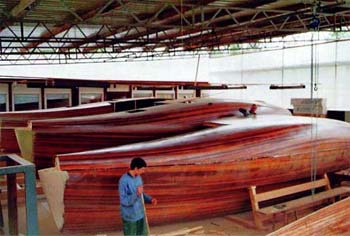
The photo below shows the bridgedeck sole being fitted. The
sole is made in foam sandwich because it is light and stiff
for the large unsupported panel area. Airex foam is very good
in impact for the odd occasion when a wave might slam up under
the bridgedeck.
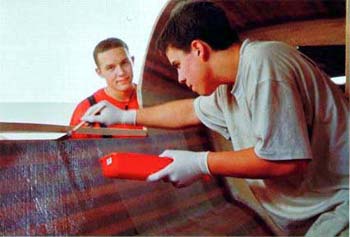
With the hull complete, the interior is fitted. Combinations
of foam sandwich and wood veneers, produce a comfortable and
beautiful look. The interior is fairly simple, with lots of
locker space, and large comfortable berths. The inside of the
hull is left with the wood showing. The lines
of the wood enhance the curved shape.
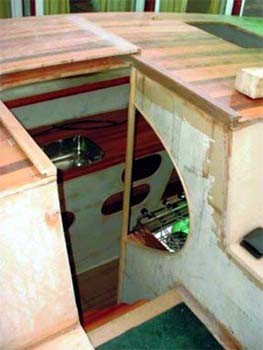
Note the aluminium backing plates behind the fittings. At
highly loaded fittings layers of unidirectional glass fan out
into the hull or bulkheads taking the loads away from highly
stressed areas into the body of the boat.
Sailing trials.
The day finally came just under two years since I posted the
plans to Switzerland, when I was asked to go to Calais in France
to help them sail the boats to Cowes on the Isle of Wight, England.
This sail was to be part of extended sailing trials to fully
assess the boats, and to help teach the crew about Multihull
sailing.
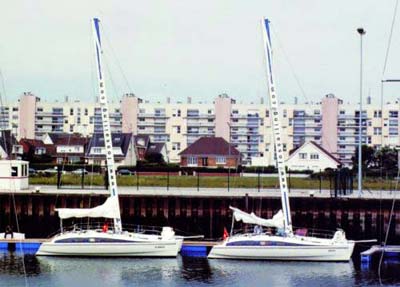
After sailing from Calais to Cowes, I spent three days sailing
the two boats in the Solent in a variety of conditions. The
boats are well built and look fantastic. Both boats sport the
racing rig with Gougeon wing masts. "We chose Gougeon because
they were the only masts we could build ourselves" said
Thomas Wolf.
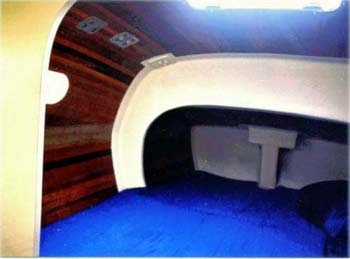
The Fossailing team have clearly demonstrated that the Shuttle
31 is a good boat for amateurs to build. They chose to use my
design for strip planked Western Red Cedar with glass fibre
on both sides and although I predicted that they would add about
230 Kgs to the weight of the boat over a foam sandwich version,
they are sure that they have added less weight by being very
careful in the laminating process.
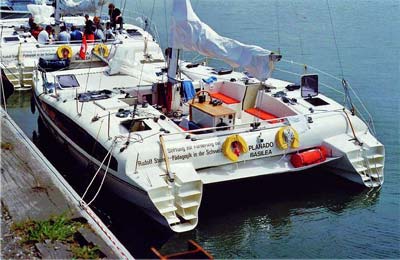
The boats float on their marks and perform very well and we
achieved 8 knots to windward tacking through 85 degrees, easily
outsailing any monohulls that we came across in the Solent as
usual. I have enjoyed the experience of sailing with this enthusiastic
group of young people and I would like to take the opportunity
to congratulate them all on a fine achievement. The boats look
good, and I am sure they will have many years of enjoyable and
fun sailing on them."