*(Big
Honkin’ Sandin’ Block)
One day I put a brand
new belt on my trusty 3x24 belt sander and got to
work fairing some things out. Then I hit a snag, literally.
I missed a screw that was still poking sharp point
out and it cut my new belt into two small belts which
then proceeded to slap me silly. After I got done
throwing things and swearing, I put another new belt
on and finished sanding. Later in the day I was cleaning
up a bit and started to throw the ruined belt in the
garbage and I decided I ought to find a way to use
what remained. The BHSB is what I came up with, they’ve
worked out so well that I make them with new unused
belts now.
Step
1:
You’ll want to cut the belt in half, and then
cut out the taped joint. Believe me when I say this
taped joint is NOT strong enough to survive what
we are going to do to it later.
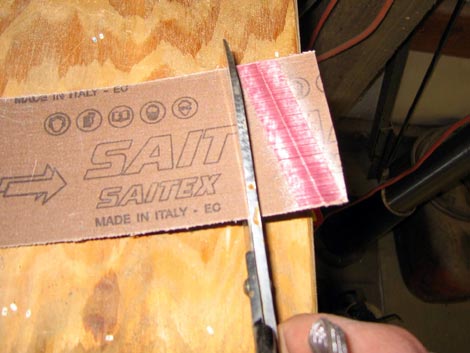
Step
2:
You’ll need to mill up a top and bottom board
and then a couple clamp/spacers. I usually mill
everything so that they are about 1/8 of an inch
or so narrower than the belt I’m planning
on using so that the belt can flex some up both
sides by about a 1/16th. The top and bottom boards
get cut to about 4” or so less in length than
the belt. Cut the bottom board in half, and attach
one of the spacers at the joint on one side only.
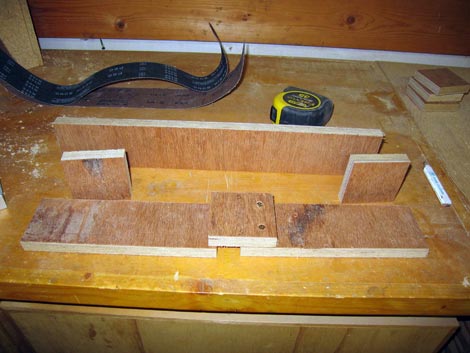
Step 3:
Wrap the belt up and over
the end of one of the bottom boards and then clamp
it down with a couple screws through the spacer
block
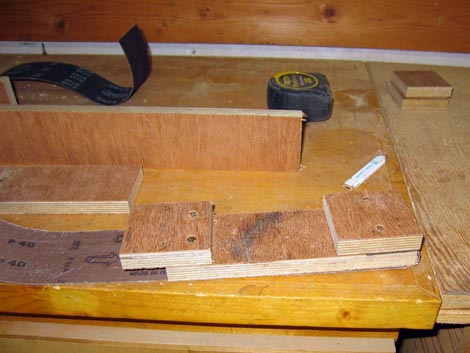
Step 4:
Next step is to attach the
other side of the belt to the other board. You’ll
want to do it such that there is a slight gap under
the joint, this is where the tension will come from
later. I’ve found a 1” to 1 ½”
gap (ie two pieces of 3/4” plywood) is just
about perfect. If it’s too tight the belt
will tear so don’t overdo it. Once the belt
is attached then line the two bottom boards up and
get it set up like this.
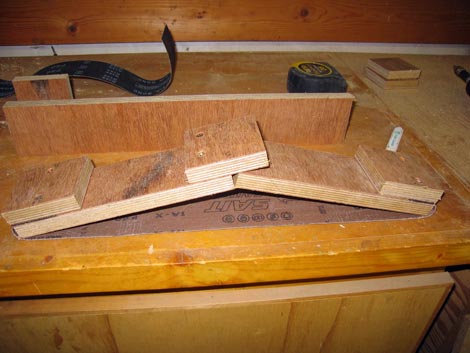
Step 5:
Push down in the middle until
the middle block makes contact and screw it down.
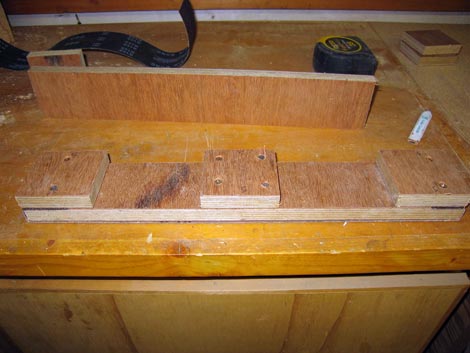
Step 6:
Sand the top and bottom edges
of the top board so that you have a nice smooth
edge to hang on to. Countersink the screw holes
and screw it down to the spacers. Make sure that
you set your screws so that they don’t run
into the tops of the ones holding the spacers to
the bottom board.
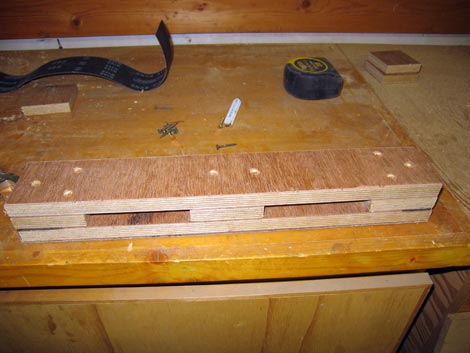
You are off and running. I’ve
found that having a couple in different widths and
grits makes short work of shaping and fairing things.
Because the belt is under tension it stays nice and
flat against the bottom board and doesn’t deflect
or bunch up.
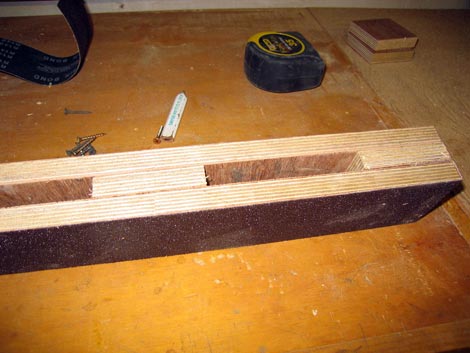
|